Table of Contents
ToggleIntroduction
Welding plays a foundational role in industrial valve construction, ensuring structural integrity, leak-proof performance, and long-term durability. In demanding sectors like oil, chemical processing, and power generation, the quality of valve welding directly impacts system safety and efficiency.
Gowin, as a representative of precision engineering, has been serving these high-requirement industries for years, offering valve welding solutions that stand up to the toughest conditions.
The Critical Functions of Valve Welding
Valve welding serves multiple purposes beyond simple connection. By welding valve bodies, bonnets, and flanges together, it enhances overall strength, reduces part redundancy, and allows for compact designs—particularly useful in pipe-dense environments.
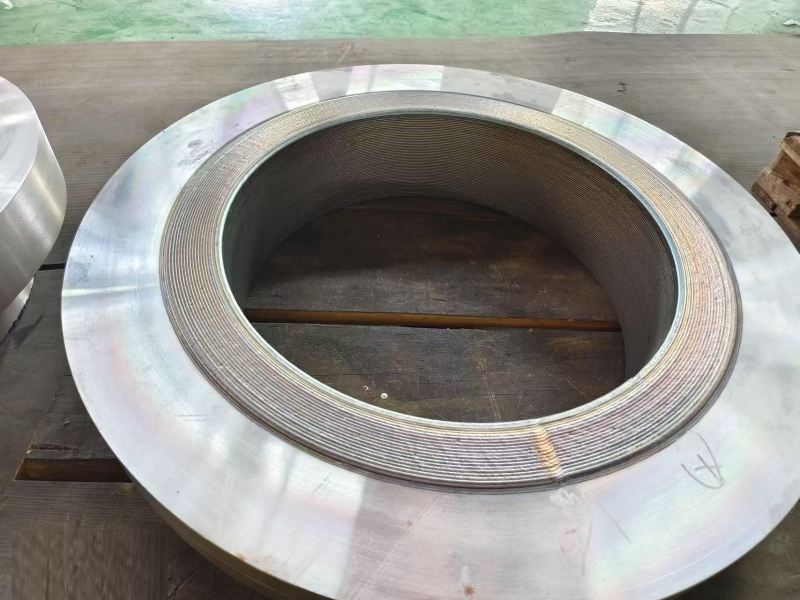
Welding also ensures better sealing performance. Seamless joints prevent leaks in high-pressure, high-temperature, and corrosive systems. Technologies like TIG (Tungsten Inert Gas) welding and automatic surfacing allow precise weld control. Gowin applies a two-layer surfacing process with a final weld thickness of ≥3mm, improving corrosion resistance, mechanical strength, and sealing integrity.
Additionally, Gowin’s welding processes are highly adaptive, handling stainless steel, alloy steel, titanium alloy, and even dissimilar materials. This flexibility enables broader application in low-temperature or strongly corrosive conditions, such as those in chemical or offshore environments.
Welding Valve Types: Practical Applications
Gowin applies its welding expertise across a wide range of valve products. Whether it’s welding check valve, welding gate valve, or welding butterfly valve, each undergoes rigorous process control to ensure precision and performance. For instance, our check valve welding techniques are optimized for one-way flow control under fluctuating pressures, while welding butterfly valves require specialized joint designs for compact and lightweight operation.
For pressure-bearing parts, Gowin uses processes like submerged arc welding (SAW) and MIG welding to achieve deep penetration and low defect rates. Surfacing with corrosion-resistant alloys such as Inconel further extends the lifespan of sealing surfaces.
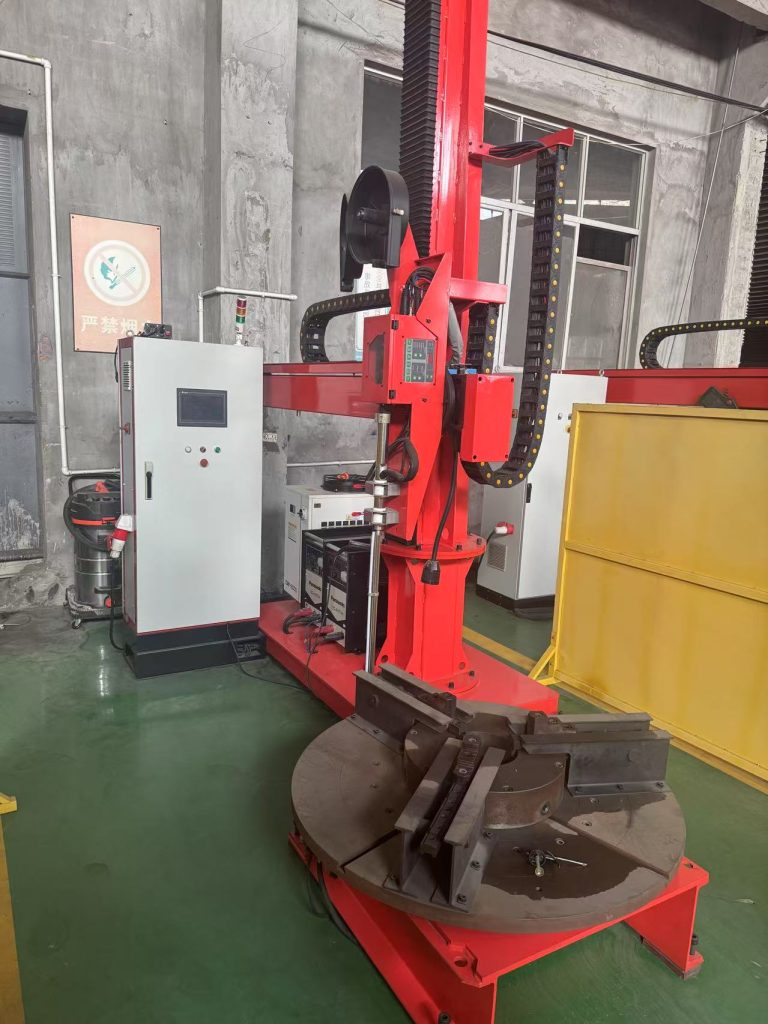
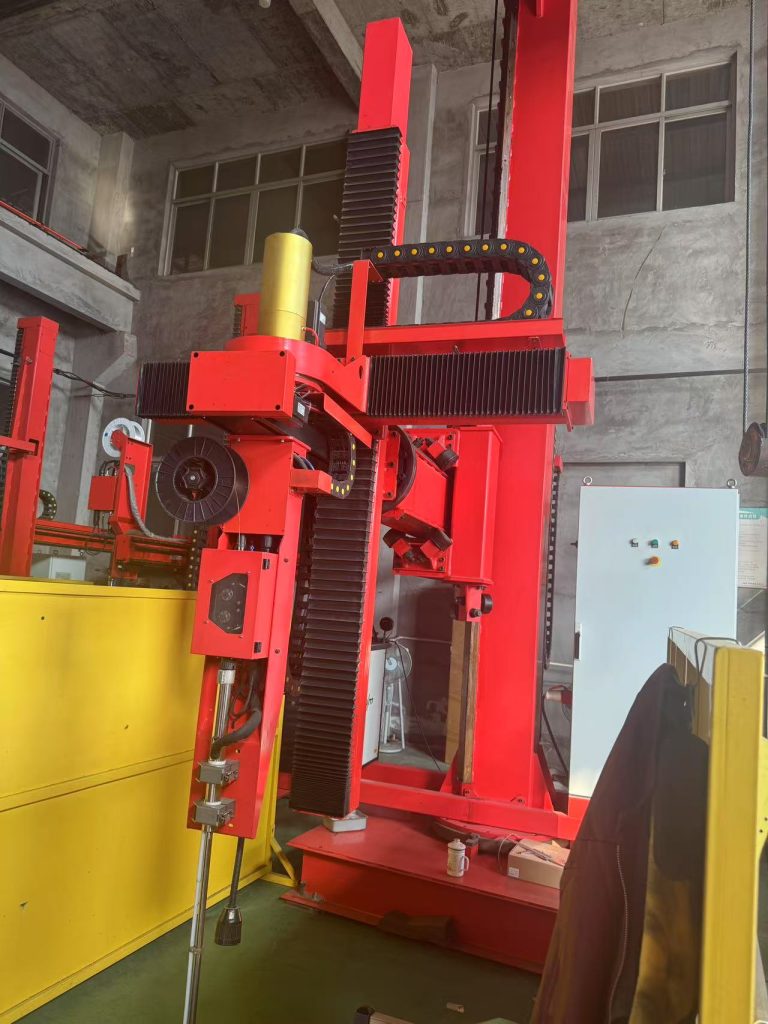
Welding Certification and Quality Assurance
Gowin ensures every weld meets global standards. Our welders are certified by third-party agencies and safety bureaus with official operation licenses. More importantly, all valve welding processes conform to international standards including API 6D, ISO 9001, and ISO 14001.
We also perform non-destructive testing (NDT), such as X-ray inspection and ultrasonic testing, to detect internal defects and ensure weld density and reliability.
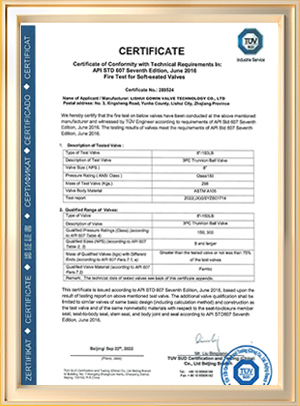
Repair, Upgrades, and Cost Efficiency
Welding not only enhances new valve production but also enables cost-effective repairs and upgrades. Techniques like laser cladding or TIG-based overlay can restore damaged sealing surfaces without replacing entire valves. Gowin also performs welding modifications—such as adding sensor ports or bypass lines—helping clients upgrade systems without full replacements.
With automated welding lines, Gowin reduces production time and enhances consistency, ensuring high-efficiency delivery for bulk valve projects.
Conclusion
Valve welding is both a science and an art—requiring precision, experience, and certification. Gowin’s expertise in valve welding, backed by international certifications and advanced techniques, ensures our welding check valves, welding butterfly valves, and welding gate valves meet the demanding expectations of global industries.
As the industries evolve, Gowin continues to push boundaries, offering reliable welding solutions that protect system integrity, safety, and longevity.