Table of Contents
ToggleTriple eccentric butterfly valves are high-performance flow control solutions designed for demanding industrial applications requiring tight sealing, durability, and efficiency.
Their unique geometry eliminates common sealing issues seen in standard butterfly valves, making them a preferred choice in high-pressure and high-temperature environments.
In this article, we’ll break down how these valves work, where they shine, and why Gowin’s advanced product line—including tri-eccentric butterfly valves—has earned its place in major industries such as petrochemical, offshore platforms, and power generation.
What is a Triple Eccentric Butterfly Valve?
Also known as a triple offset valve butterfly design, this valve is a significant evolution over conventional concentric and double eccentric butterfly valves.
The “triple eccentric” name refers to the three key deviations from the centerline:
- The first offset is between the shaft and the seat centerline.
- The second is between the shaft and the pipe centerline.
- The third offset involves the cone angle of the sealing components, allowing a cam-like motion.
This design reduces friction during operation and ensures a non-rubbing, torque-seated closure.
The result?
An exceptionally tight, zero-leakage seal even under extreme thermal and pressure conditions.
Why the Triple Offset Design Matters
Unlike standard butterfly valves, the triple eccentric butterfly valve’s geometry ensures the disc does not scrape or drag across the seat.
This cam-style closure action enhances service life and minimizes wear—two crucial factors in facilities that operate continuously under stress, like offshore rigs and chemical processing units.
Additionally, this design allows for metal-to-metal sealing, making the valve fire-safe and compatible with high-temperature and corrosive environments.
That’s a game-changer in industries where synthetic polymers or caustic chemicals are in constant flow.
Triple Offset Geometry in Detail
The unique valve gate configuration in triple eccentric butterfly valves eliminates the weaknesses of traditional rubber-seated valves.
The third offset—the inclined cone angle—ensures the sealing surfaces only engage at the final point of closure.
This prevents scraping, reduces seat wear, and provides excellent repeatability in opening and closing cycles.
This geometry allows for higher pressure ratings, reduced torque requirements, and greater operational consistency across varying process conditions.
It also supports zero-leakage sealing standards, which is vital for industries dealing with flammable or toxic media.
Advanced Sealing Technology
One of the key strengths of triple eccentric butterfly valves is their ability to maintain a bubble-tight seal even after thousands of cycles.
The metal-to-metal sealing construction, often incorporating hard-faced materials like Stellite or Inconel, provides long-lasting reliability.
This superior sealing is particularly useful in gas-tight and fire-safe applications.
In power generation or refinery settings where fluid isolation is mission-critical, the tight seal offered by tri-eccentric valves prevents backflow, contamination, and energy loss.
Gowin’s butterfly valves are built with precision-machined sealing surfaces and customizable seat materials based on specific project requirements.
This commitment to sealing integrity makes them a trusted solution for performance-critical applications.
Material Selection for Harsh Environments
When it comes to flow control in corrosive or abrasive environments, material selection can make or break valve performance.
Gowin offers triple eccentric butterfly valves constructed from a wide range of materials, including stainless steel, duplex, Hastelloy, and Monel.
For offshore applications, corrosion resistance is paramount due to exposure to saltwater and harsh weather.
In chemical plants, resistance to acids, alkalis, and volatile organic compounds is equally essential.
Gowin’s material flexibility allows engineers to select the optimal valve composition for their exact needs—minimizing downtime and maximizing operational safety.
Lifecycle Efficiency and Maintenance
Compared to traditional valve designs, triple offset butterfly valves offer a distinct advantage in maintenance and longevity.
The non-rubbing closure design means less wear and tear, which translates to longer service intervals and reduced maintenance costs.
These valves also tend to be lighter and more compact than equivalent gate or globe valves, which simplifies installation and reduces structural load on piping systems.
In remote locations like offshore platforms, these factors are crucial.
Gowin supports its valves with thorough documentation, easy-to-service designs, and after-sales engineering guidance.
This ensures that end-users can maintain their systems efficiently, even in high-risk or logistically challenging environments.
Customization and Engineering Support from Gowin
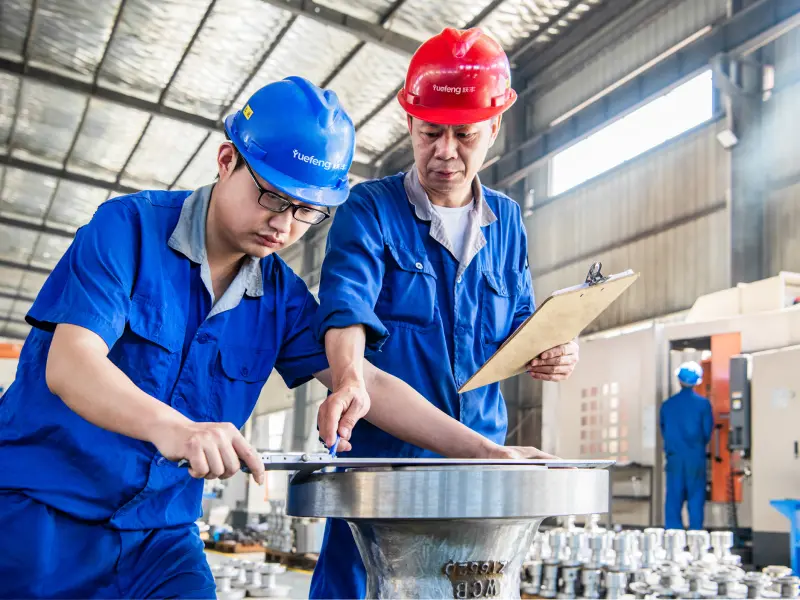
Every plant and pipeline has its own set of challenges, and a one-size-fits-all valve approach often falls short.
Gowin addresses this by providing engineering customization services for its triple eccentric butterfly valves.
Whether it’s adapting the valve for cryogenic service, integrating actuation systems, or meeting region-specific compliance codes, Gowin offers flexibility at every stage.
This engineering adaptability has allowed Gowin to support clients across industries—from customizing triple offset butterfly valves for refinery upgrades to delivering high-performance valves for subsea installations.
Purchasing managers and system designers benefit from Gowin’s deep technical experience and willingness to tailor solutions.
Why Choose Triple Eccentric Butterfly Valves?
The benefits of tri-eccentric butterfly valves are clear when compared to other valve types in similar pressure classes:
- Superior sealing with no compromise on repeatability
- Minimal seat wear due to cam-action closure
- Fire-safe and gas-tight designs for hazardous media
- Compact, lightweight structure for easier handling
- Wider operating range including high-pressure, high-temperature, and corrosive media
For operations that require precision, safety, and efficiency, such as petrochemical refineries and power generation units, these valves offer long-term value and peace of mind.
Industry Applications Where Performance Matters
Gowin’s triple eccentric butterfly valves are not just theoretical innovations—they’re battle-tested in some of the world’s most challenging environments.
Let’s take a look at where they’ve made a significant impact:
- Petrochemical Projects: Safely isolating and regulating hazardous chemicals under pressure.
- Offshore Platforms: Handling saltwater exposure, mechanical vibrations, and high flow rates with ease.
- Power Plants: Providing reliable shutoff in steam and cooling water systems under intense temperatures.
These real-world applications validate Gowin’s position as a reliable manufacturer not just of basic valve components, but of premium engineered solutions.
Summary: Innovation, Durability, and Trust
Triple eccentric butterfly valves are the gold standard for industrial flow control, where performance cannot be compromised.
Their unique sealing mechanism, material flexibility, and operational efficiency set them apart from conventional options.
Gowin goes beyond standard offerings by delivering innovative tri-eccentric butterfly valve solutions designed to perform under pressure—literally.
Whether you’re running a refinery, offshore platform, or thermal power plant, Gowin’s expertise and full-spectrum product line mean that the right valve is never out of reach.