Table of Contents
ToggleSelecting the appropriate valves for chemical and petrochemical plants is paramount to ensuring operational efficiency, safety, and longevity.
These industries handle a myriad of corrosive and high-pressure substances, necessitating valves that can withstand such demanding environments.
Understanding the nuances of valve selection, material compatibility, and application-specific requirements is crucial for optimal plant performance.
Understanding the Role of Valves in Chemical and Petrochemical Industries
Valves serve as critical components in controlling the flow, pressure, and direction of fluids within processing systems.
In chemical and petrochemical facilities, valves control the flow of harsh chemicals, heat-intensive fluids, and reactive substances essential to operations.
The correct valve selection plays a critical role in ensuring safe and efficient process management.
The right valve ensures not only efficient flow control but also the safety of the entire operation.
Key Considerations When Selecting Valves
Material Compatibility
The valve material must resist corrosion and degradation when exposed to specific chemicals. Materials like stainless steel, Hastelloy, Monel, and PTFE linings are often chosen for their resilience.
Operating Conditions
Valves must function effectively under the plant’s specific temperature and pressure conditions.
Valves constructed from materials like PVC or PVDF are highly resistant to corrosive chemicals, although they typically fall short in environments involving elevated temperatures.
Flow Control Requirements
Depending on whether the application requires throttling, isolation, or backflow prevention, different valve types like globe, gate, or check valves may be appropriate.
Maintenance and Durability
Valves should offer longevity with minimal maintenance. Features like self-cleaning capabilities or designs that reduce wear can enhance durability.
Compliance and Standards
Valves should adhere to industry standards and certifications, ensuring they meet safety and performance benchmarks.
Types of Valves Suitable for Chemical and Petrochemical Applications
Valve Type | Functions |
Ball Valves | Ball valves are widely chosen for their reliable sealing capabilities and rugged performance, making them particularly effective for isolation duties in fluid systems. They handle a variety of fluids, including slurries and viscous substances. |
Butterfly Valves | These are lightweight and cost-effective, suitable for large-volume flow control. Their compact design makes them ideal for systems with space constraints. |
Diaphragm Valves | Featuring a flexible diaphragm, these valves are excellent for handling corrosive and abrasive fluids, preventing contamination and ensuring clean operation. |
Globe Valves | Effective for throttling applications, globe valves provide precise flow control, making them suitable for processes requiring accurate regulation. |
Check Valves | Designed to prevent backflow, check valves ensure unidirectional flow, protecting equipment from potential damage. |
Needle Valves | These allow fine control over flow rates, making them ideal for applications requiring precise adjustments. |
Importance of Corrosion-Resistant Valves
Corrosion is a significant concern in chemical processing. Using corrosion-resistant valves extends equipment life and ensures safety.
Materials like PTFE, PFA, and other fluoropolymers are commonly used linings to protect valves from aggressive chemicals.
These linings act as barriers, preventing the fluid from contacting the metal parts of the valve.
Valves for the Petrochemical Industry
The petrochemical industry deals with the processing of hydrocarbons, requiring valves that can handle high pressures and temperatures. Valves for the petrochemical industry must be robust and reliable. Common types include gate valves, globe valves, and check valves. These valves are designed to manage the flow of petrochemical fluids safely and efficiently.
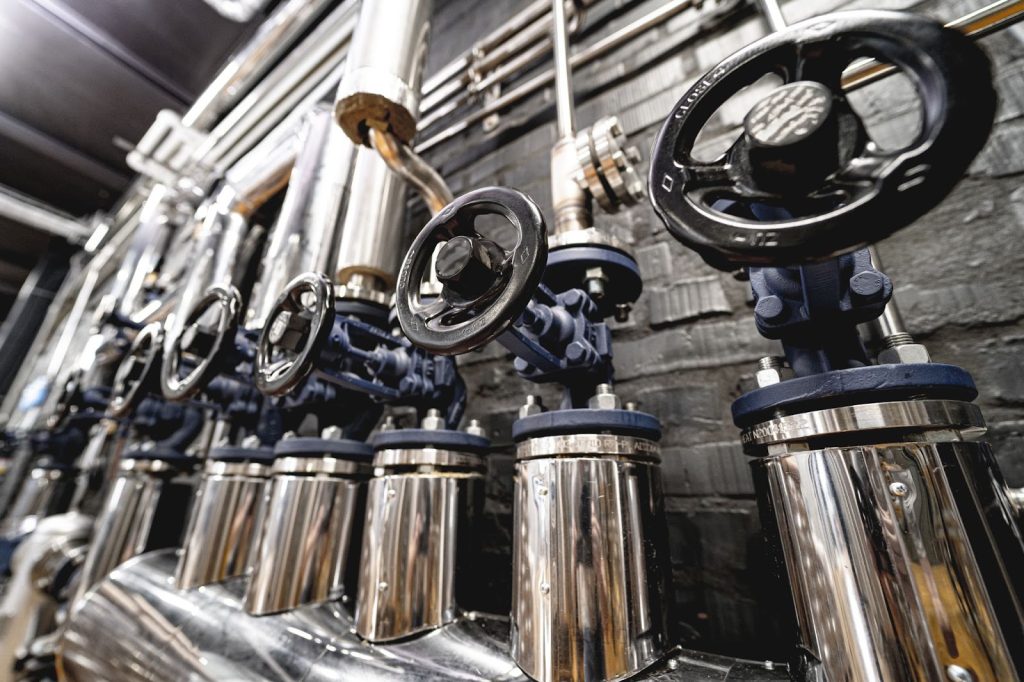
Automation and Smart Valve Integration
The integration of smart valve technologies is revolutionizing the chemical and petrochemical industries.
Advanced valve positioners and actuators equipped with digital communication protocols like HART and Foundation Fieldbus enable real-time monitoring and precise control of fluid systems.
These intelligent systems facilitate predictive maintenance by detecting anomalies early, thereby reducing unplanned downtime and maintenance costs.
For instance, smart valve positioners can automatically adjust valve positions to maintain optimal flow rates, enhancing process efficiency and safety.
Implementing smart valves also supports remote operation capabilities, allowing operators to control and monitor valve performance from centralized control rooms.
This not only improves operational efficiency but also enhances safety by minimizing the need for manual intervention in hazardous areas.
Valve Testing and Certification Requirements
Ensuring that valves meet stringent industry standards is critical for safe and reliable operations in chemical and petrochemical plants.
Valves must undergo rigorous testing and obtain certifications such as API (American Petroleum Institute) standards, ISO 15848 for fugitive emissions, and TA Luft for air pollution control.
These certifications verify that valves can withstand the demanding conditions of chemical processing, including high pressures, temperatures, and corrosive media.
To ensure valves continue to function properly, scheduled inspections and upkeep are necessary throughout their service life.
Hydrostatic testing, seat leakage tests, and functional testing should be conducted periodically to ensure valves perform as intended.
Maintaining detailed records of these tests helps in compliance with regulatory requirements and facilitates timely maintenance actions.
Environmental and Safety Compliance
Valves play a pivotal role in ensuring environmental protection and safety in chemical and petrochemical industries.
Choosing the right valve and maintaining it diligently helps minimize leaks and hazardous discharges, safeguarding both workers and surrounding ecosystems.
Meeting compliance standards, like those outlined in LDAR protocols, often requires using valves designed to limit fugitive emissions.
Safety considerations also dictate the use of valves with fail-safe features, such as emergency shut-off capabilities and pressure relief mechanisms.
These features are crucial in preventing accidents and ensuring safe shutdowns during emergency situations.
Selecting valves that meet Safety Integrity Level (SIL) requirements further enhances the safety profile of the plant.
Maintenance and Lifecycle Cost Analysis
Considering the full lifecycle expenses of a valve—from acquisition to maintenance and replacement—is vital when aiming for operational efficiency and long-term value.
While the initial purchase price is a consideration, factors such as maintenance costs, energy consumption, downtime, and lifespan significantly impact the overall cost.
Investing in high-quality, durable valves may entail higher upfront costs but can result in substantial savings over time due to reduced maintenance and longer service life.
Implementing a lifecycle cost analysis (LCCA) approach enables plant managers to make informed decisions by comparing the long-term costs associated with different valve options.
This analytical method considers all costs from acquisition to disposal, ensuring that the selected valves provide the best value over their operational life.
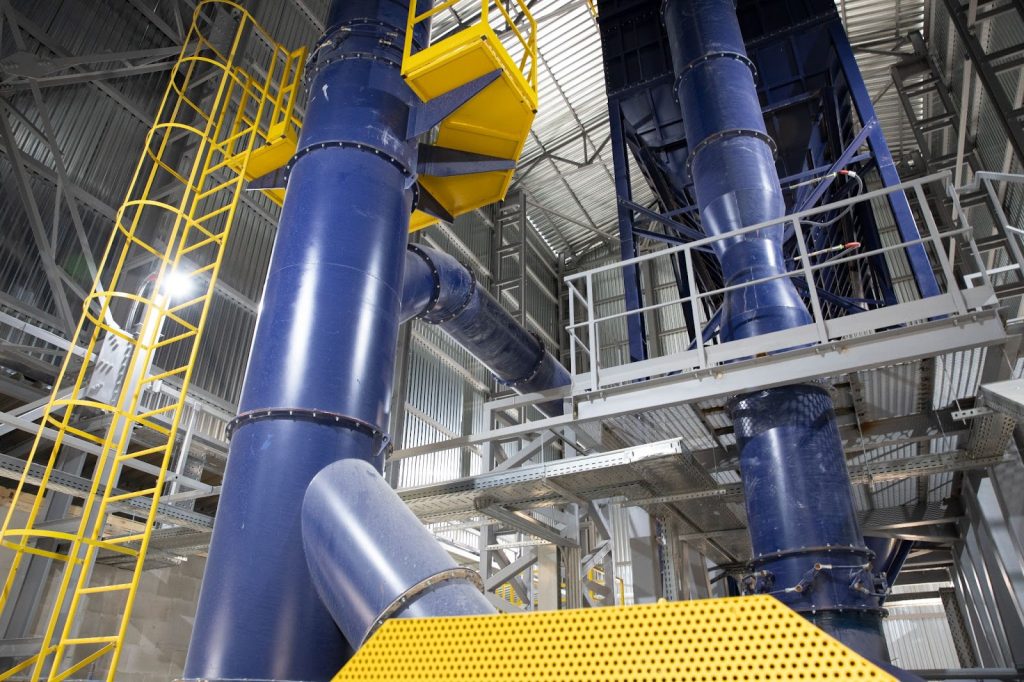
Gowin: A Trusted Valve Manufacturer for the Petrochemical Industry
Gowin has built a strong reputation as a trusted supplier of valves tailored for the specific demands of the petrochemical sector.
Their range of products includes ball valves, butterfly valves, diaphragm valves, and needle valves, all designed to handle different corrosive media.
Gowin’s “multi-functional adjustment” capability allows their valves to be customized for various applications, ensuring optimal performance.
Gowin’s valves have been successfully implemented in several petrochemical projects, demonstrating their reliability and efficiency.
Their commitment to quality and innovation makes them a preferred choice for purchasing managers in the chemical industry.
Final Thoughts on Choosing Valves for Chemicals
Choosing the right valves for chemical and petrochemical plants is a decision that impacts safety, efficiency, and cost-effectiveness.
By considering factors like material compatibility, operating conditions, and maintenance requirements, industries can select valves that meet their specific needs.
Gowin stands out as a Chinese industrial valve manufacturer that purchasing managers in the chemical industry can trust, offering a range of products designed for durability and performance in challenging environments.